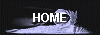
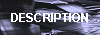
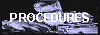


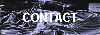
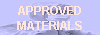
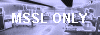
|
1.
Molecular Contamination Monitoring
At M.S.S.L. there
has been a requirement to monitor molecular contamination levels of
optical instruments, which operate over the wavelength range of 160nm
to 550nm. To this end we have introduced a molecular contamination
monitoring program utilising an PMS AiM100 Surface Acoustic Wave (S.A.W)
instrument. This instrument is used to monitor, in realtime, airborne
molecular contamination (AMC), its deposition rate and total mass
deposition on the surface of interest in either ng/cm² or Angstrom
units.
The SAW instrument
allows us to detect the deposition of AMC on a silicon dioxide sensor
surface. Due to realtime data collection we can pinpoint exactly at
what time the contamination event occured, the contamination layer
thickness and correlate optics surface damage with either internal
cleanroom activities, external events or process activities. Being
able to do this we can then eliminate or control the sources of the
AMC. In addition to this we can also investigate futher as to what
chemical species make up the contamination layer by subjecting the
SAW sensor chip to Time Of Flight/Secondary Ion Mass Spectroscopy
(TOF/SIMS) analysis
Method
of Measurement
The SAW instrument
is positioned near a critical item or process surface where the effects
of molecular contamination can result in the degradation of the instrument
or item performance.
The method of
measurement is based on the fact that a quartz crystal has piezoelectric
characteristics. The quartz crystal will oscillate when electricity
is passed through it. Both sensors (one sensor is sealed and the other
is exposed) in the PMS AiM100 are made of quartz cryastal. The crystals
top surfaces are coated with silicon dioxide and facilitates the adsorbtion
of AMC. Once AMC is adsorbed onto the Silicon dioxide surface the
crystals frequency of oscillation will be less than that of the uncontaminated/sealed
crystal. The oscillation frequency will gradually decrease as the
mass of the deposited contamination increases. The AiM100 will then
calculate the difference in frequency between the exposed sensor chip
and the reference (sealed) sensor chip. As mass accumulates on the
exposed sensor the difference in frequency between the two crystals
will increase proportionately. A software algorithm calculates the
mass of the contamination based on this frequency shift and then output
to a computer monitoring the data within the cleanroom.
Data
Archiving
Both data and
data analysis are archived on the dedicated cleanroom computer and
is made available on the cleanroom website. Click
here (MSSL only) to view the latest SAW data
2.
Non Volatile Residue monitoring (NVR)
The MSSL cleanroom
is monitored for background NVR using ASTM E 1235-95 and ASTM E 1234
- 94 methods. Results of background NVR for the MSSL cleanroom can
be found
here (MSSL only)
3.
Particulate Contamination Monitoring
This document
describes the procedure used at MSSL for the monitoring of Airborne
particulate contamination in the Cleanroom
Procedures
used in particulate monitoring
Particulate contamination
monitoring is carried out using an independently calibrated, cleanroom
dedicated, particle detector with the following specification:
Instrument: |
Climet CI-7300 microprocessor based six channel airborne particle
counter |
Particle
sensitivity: |
0.3 micron to 10 microns |
Particle
discrimination: |
0.3, 0.5, 0.7, 1, 5 and 10 microns |
Standard
sample flow rate: |
1.0 cubic ft per minute (1 CFM) |
Calibration: |
Every six months by independent contractors |
|
|
The cleanroom
is continuously monitored for particulate contamination and is logged
to a cleanroom dedicated computer via RS 232 communications. This
continuous monitoring involves taking a sample of 1 cubic ft of cleanroom
air every 3 minutes, analysing it for particles in the above mentioned
ranges and sending the results to a dedicated cleanroom computer for
monitoring and data archiving. The monitoring of the the results is
done via remote link up to the dedicated cleanroom computer using
Norton PCanywhere. This negates the need for monitoring personnel
to enter the cleanroom for monitoring purposes.
The continuous
monitoring takes place at a static reference point located near the
entrance to the cleanroom.
If levels of contamination
are seen to rise, then the particulate contamination will be monitored
at numerous locations within the cleanroom to isolate the source.Corrective
action will then be taken. The procedure for this is detailed below.
Isolating
particulate contamination sources
- Starting in
area A of the white cleanroom (closest to the HEPA filters) the
particle detector is setup and readings are taken from four different
locations in area A at a height of approximately one meter.
- At each location
four counts are taken from the four different locations, giving
sixteen counts for area A.
- At each location,
after four counts are taken, the particle detector will automatically
generate an average reading of the four counts. Whilst this is happening,
the detector inlet funnel is moved to the next location ready for
the next four counts.
- This procedure
is then repeated for areas B, C, the anteroom and the dark Cleanroom.
- Overall, 100
counts are taken for both the white and dark Cleanroom and the anteroom.
The results are then examined and appropriate actions taken if necessary.
- The results
are filed for record purposes. (see file records below)
- The following
particulate sizes are recorded together with date and time:
- 0.3 um, 0.5
um, 0.7 um, 1.0 um, 5.0 um and 10 um.
Particlate counts
are archived on the cleanroom computer and are accessed for analysis
of particulate levels.The records are saved as ASCII files and can
be imported into a word processor or spreadsheet for trend analysis
etc.
A cleanroom particulate
count archive can be found
here.
Note: some
of these files are 2Mb + so will take some time to show on a slow
connection
4.
Particulate fallout monitoring
The MSSL cleanroom
is frequently monitored for particulate fallout to ASTM E 1216 - 99
methods. Particulate fallout data for the MSSL cleanroom can be found
here.
©MSSL
Created by Alex Rousseau last
modified:
February 2, 2004 11:50
|